Operations & Supply Chain Management
Overview
Day 4 of the Five-Day MBA Programme focuses on operations management and supply chain strategy, vital components for delivering products and services efficiently while maintaining quality and cost control. In a globalised and competitive environment, businesses need to optimise their operations and build resilient supply chains to succeed. This session covers the principles of operations management, process improvement, supply chain strategy, and the use of technology to enhance operational efficiency.
Throughout the day, participants will learn how to manage operations for maximum productivity, control costs, improve quality, and mitigate risks in the supply chain. Practical workshops and real-life case studies will allow participants to apply their knowledge to real-world business challenges.
Learning Outcomes
Understand the key principles of operations management and how to optimise business processes.
Learn how to design and improve workflows for greater efficiency and quality.
Gain insights into capacity planning and resource allocation for optimal performance.
Understand the components and challenges of supply chain management in a global context.
Learn how to manage inventory effectively and balance stock levels with cost control.
Develop strategies to identify and mitigate supply chain risks and ensure business continuity.
Gain an understanding of quality management systems and how to maintain high standards.
Explore how technology can enhance operations management and improve efficiency.
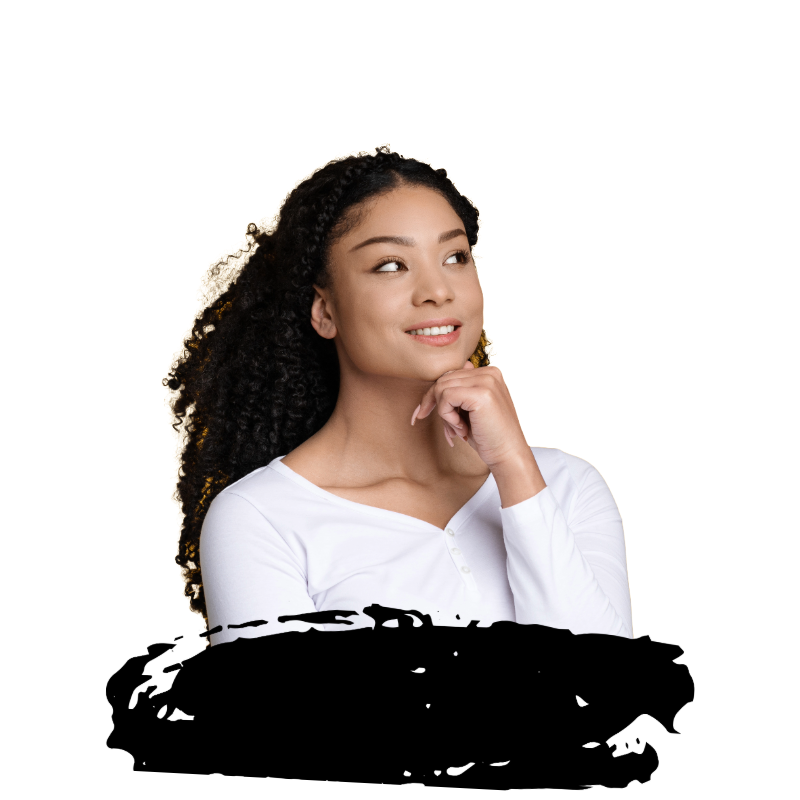
1. Introduction to Operations Management
Objective
To introduce participants to the fundamental concepts of operations management, highlighting its role in creating value and driving efficiency in organisations.
Key Concepts
Defining operations management and the process of transforming inputs into outputs
The role of operations in delivering customer value
Key operations management decisions for capacity, facilities, quality, and inventory
Aligning operations strategy with overall business objectives
Discussion Points
How can operations management help a company gain a competitive advantage?
What role does efficiency play in enhancing customer satisfaction and profitability?
Outcome
Participants will understand the core functions of operations management and how it contributes to organisational success.
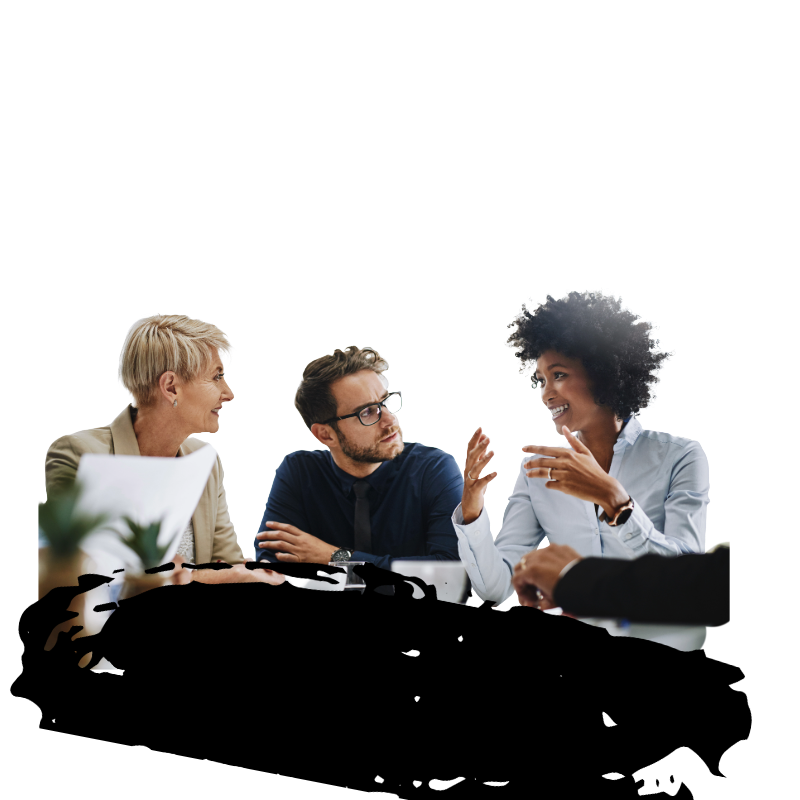
2. Process Design and Improvement
Objective
To provide participants with tools for designing and improving business processes to enhance efficiency and quality.
Key Concepts
Process mapping Visualising workflows and identifying bottlenecks
Lean management principles Reducing waste and optimising flow
Six Sigma methodology Reducing defects and improving quality
Continuous improvement The role of Kaizen in process innovation
Workshop
Participants will work in groups to map out a business process and identify areas for improvement using lean and Six Sigma tools. They will propose solutions for streamlining the process and improving quality.
Outcome
Participants will learn how to analyse and improve business processes, enhancing operational efficiency and effectiveness.
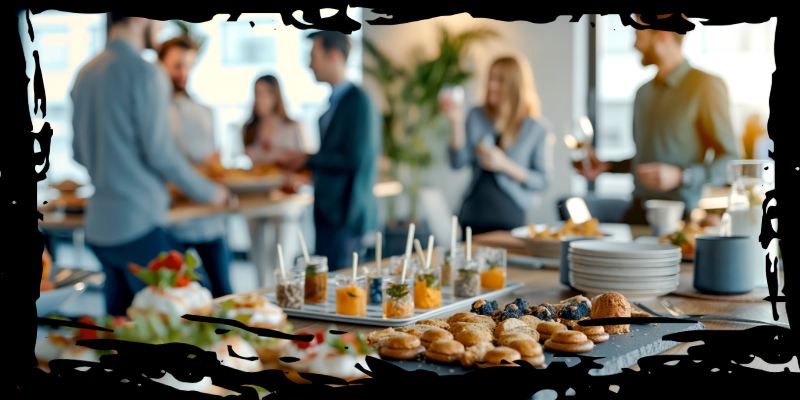
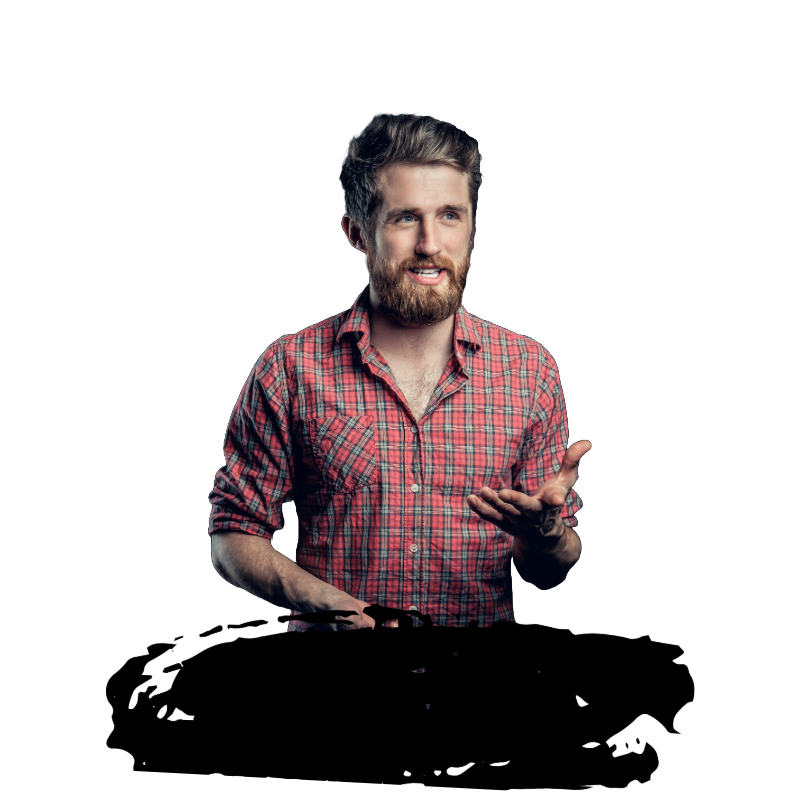
3. Capacity Planning and Resource Allocation
Objective
To help participants understand the importance of capacity planning and resource allocation in meeting customer demand efficiently.
Key Concepts
Capacity planning Matching supply with demand
Balancing utilisation, productivity, and flexibility
Resource allocation Optimising workforce, equipment, and facilities
Managing variability in demand and lead times
Case Study
Participants will analyse a company’s capacity planning approach and discuss how fluctuations in demand impact resource allocation and operational efficiency.
Outcome
Participants will gain insights into how to manage capacity and resources to ensure smooth operations and meet customer expectations.
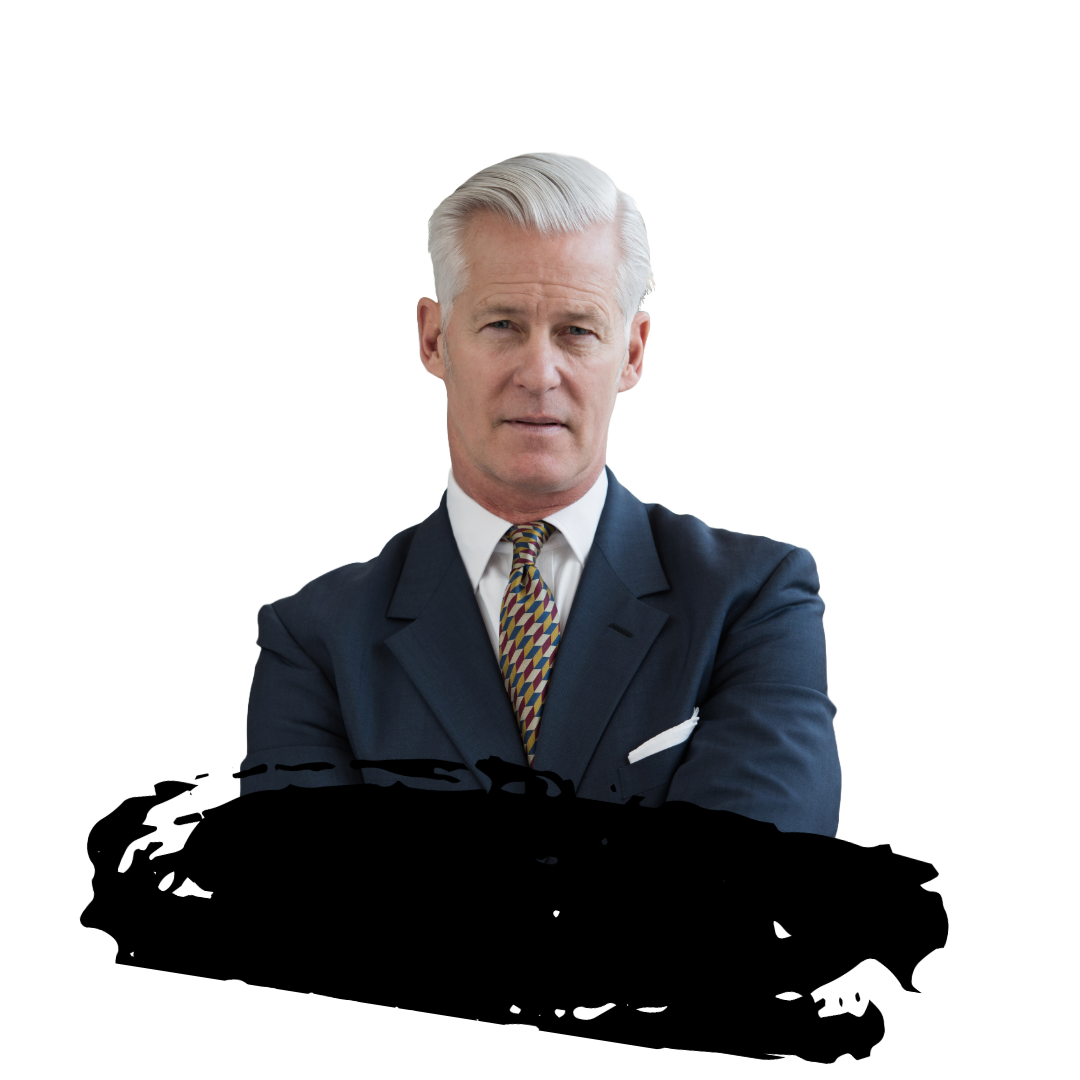
4. Supply Chain Management Fundamentals
Objective
To introduce participants to supply chain management and its role in delivering products and services to customers efficiently.
Key Concepts
The supply chain Key components and stages, from raw materials to end customer
Supply chain optimisation Improving efficiency and reducing costs
Managing supply chain complexity in global markets
The role of technology in supply chain management (e.g., automation, AI, and IoT)
Case Study
Participants will analyse the supply chain of a global company, identifying key challenges and discussing how technology has been used to improve supply chain performance.
Outcome
Participants will learn how to manage and optimise supply chains, focusing on cost control, speed, and quality.
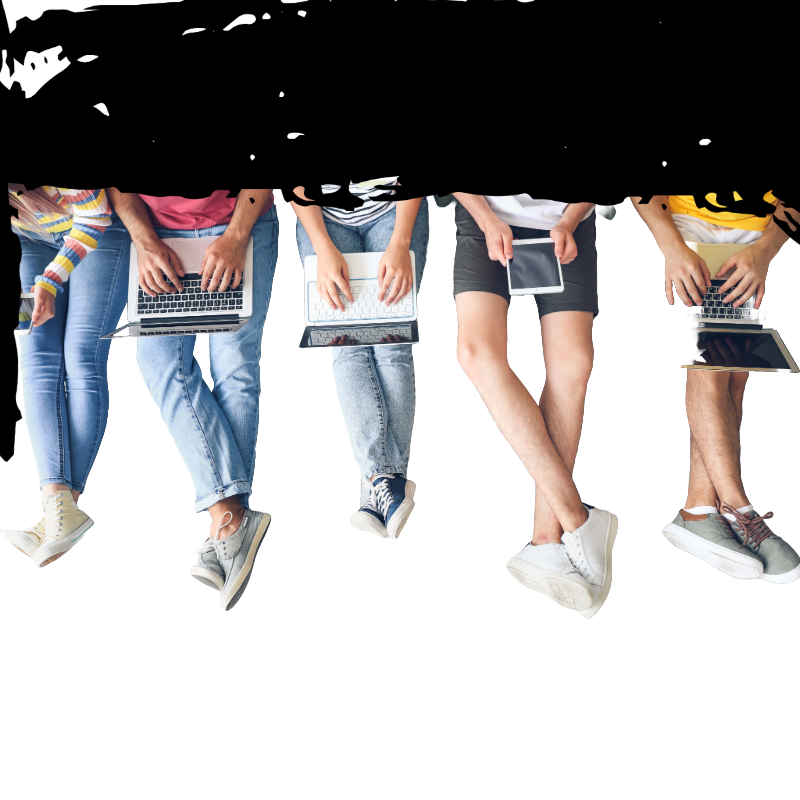
Additional Online Content
5. Inventory Management and Control
Objective
To provide participants with strategies for managing inventory effectively, balancing the need for stock availability with the cost of holding inventory.
Key Concepts
Inventory types Raw materials, work-in-progress, and finished goods
Just-in-time (JIT) inventory Minimising stock levels while meeting demand
Economic order quantity (EOQ) and reorder points Calculating optimal inventory levels
The trade-offs between holding costs and stockout risks
Workshop
Participants will work on a scenario involving a company facing inventory management challenges. They will use EOQ and reorder point calculations to develop a more efficient inventory management system.
Outcome
Participants will develop practical skills in managing inventory and reducing costs while ensuring product availability.
6. Supply Chain Risk Management
Objective
To help participants identify potential risks in the supply chain and develop strategies to mitigate them, ensuring resilience and continuity.
Key Concepts
Identifying supply chain risks Disruptions, supplier reliability, geopolitical risks, and natural disasters
Risk mitigation strategies Diversification, buffer stock, and dual sourcing
Building supply chain resilience Flexibility, transparency, and collaboration
The role of technology in monitoring and managing supply chain risks
Case Study
Participants will examine a real-world example of a company that faced a major supply chain disruption. They will discuss the lessons learned and propose strategies for mitigating similar risks in the future.
Outcome
Participants will learn how to assess and manage supply chain risks, ensuring business continuity and minimising the impact of disruptions.
Conclusion
The fourth day will conclude with a reflection session, where participants will share their key learnings and insights from the day. A Q&A session will follow, providing participants with an opportunity to clarify any concepts and discuss specific operational challenges they face in their own organisations.